What an adventure - to watch the unbuilding of the overpass. Here is a
photo-description of removing an elevated section of highway. There
were two challenges: how to take meaningful night photos and the
understand the girder removal process. For the first, I must thank
Stephen SetteDucati for some
quick lessons in night photography.
The engineering challenge is how to remove the overpass girders without
destroying the roadbed underneath. First the roadbed underneath the
overpass is covered with a blanket made of old automobile tires - to
absorb the shock associated with falling debris. In addition,
I learned from tonight's
adventure that there are two classes of machines are used: one with a hydraulic
shear for cutting the concrete girders (including the embedded rebar)
and the other, I believe is a hydraulic grapple for
holding and stabilizing a girder while it is being cut with the shears.
It also plays a role in picking up and transporting large chuncks of debris.
The overpass is supported by pairs of vertical columns (piers) with a
cap on top. The space between caps is spanned by some sort of girder -
steel or prestressed concrete. The roadbed is then built on top of
the girder structure. To remove the overpass, it seems that you just
reverse the process - roughly following this recipe:
- Remove the aluminum rails
- During the removal process, water is sprayed in the direction of
the work area to minimize dust.
- Remove the side barriers
- Push through the roadbed floor between the beams
- When all the roadbed between beams is removed, then one machine with
claws or grapple (I call it a whatever until one of you tells me the
proper name)
holds and stabilizes the beam close to one of the supporting caps. At the
same time another shearing machine (giant sissors) cuts the beam near the
edge of the pier - small bites, starting at the top and finally cutting the
last chunk (concrete with embedded rebar). The grapple machine then
slowly lowers one end of the beam until the rest sort of falls off the
other supporting cap.
- The operators of these machines then clean up the girder debris
and and move it to the side for later reprocessing. The rebar will be
separated from the concrete and pretty much everything recycled. Large
segments of concrete will be transported to the Navy Shipyard and placed
on barges and then deposited at artifical reef sites off our coast.
- When all beams are removed, the pair of near piers and cap are pushed over
with one machine cutting the base of one column while the claw machine
gently pushes the entire struture over.
Here is the overpass with side rails, supporting piers and caps -
a before view

Removing a segement of the side aluminum rail
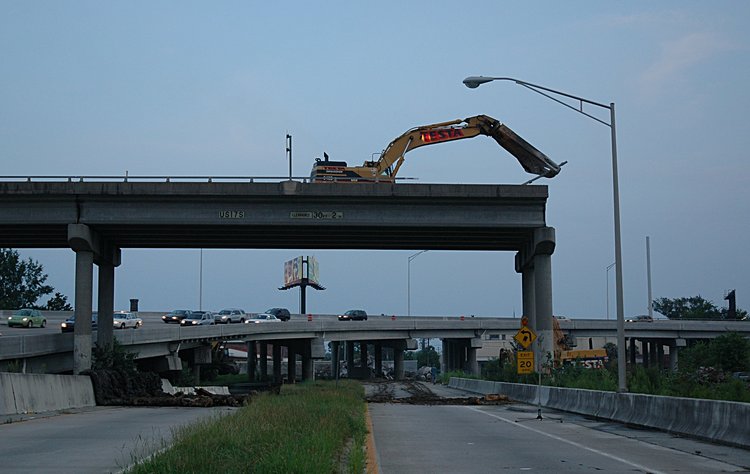
Cutting and pushing the edge barriers over the side - chunk by chunk
starting on the north side

A larger chunk on the north side

Then working on the south side - punching through the areas between girders



More punching through the floor between girders

While holding the girder with a "whatever" the hydraulic shearer takes bites
out of the first edge girder at the edge of the cap - weakening the area
over the pier cap

Shearing in action

Then gently lowering the first girder


and a little cleanup action

After some time (about 2 hours) removing the final girder:
continuing the hold and shear process

a deeper bite

and the final bite

and gently lowering the girder

down

down

to a temporary resting place - where cleanup begins again

Now that all the girders have been removed, the last step is
gently pushing the pair of piers and the cap over

The left machine is biting the cap while the right machine is right
machine is biting the base of the right column.

Jaws wide open after a gentle nudge

And then gravity does the rest of the work

and cleanup

and more cleanup

and I went home after admiring the clean interface between the next
set of girders (spanning the I-26 on-ramp) and the supporting cap.
